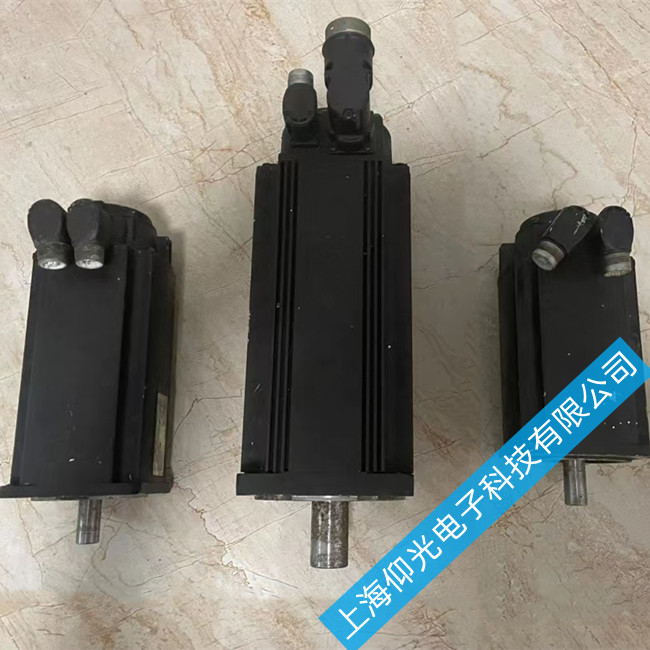
工业自动化领域伺服电机定位不准确问题频发,工控维修行业数据显示,编码器故障、驱动器参数偏差及机械结构异常已成为设备“失准”的三大核心诱因。这一现象不仅导致加工精度下降,更对产品质量和生产效率构成严重威胁。维修专家指出,企业需从硬件、软件及机械层面系统排查问题根源,通过精准维修与参数优化提升设备稳定性。
故障溯源:三大“病灶”精准定位
经工控维修团队深度分析,伺服电机定位偏差的故障原因可归结为以下三类:
编码器故障:作为伺服系统的“眼睛”,编码器常因环境振动、油污侵蚀或电子元件老化导致信号丢失或跳变,使驱动器接收的反馈位置与实际位置产生偏差;
驱动器参数设置不当:位置环增益、速度环增益等参数若与负载特性不匹配,将引发电机响应滞后或超调,最终表现为定位误差;
机械结构问题:传动链磨损(如联轴器间隙)、丝杠松动或导轨变形等机械故障,会放大伺服系统的控制误差,形成“硬件-软件”双重干扰。
维修攻坚:三步破解“定位困局”
针对上述故障,工控维修专家提出分级解决方案:
第一步:编码器“精准修复”
通过示波器监测编码器输出波形,使用编码器测试仪检测零位脉冲及分辨率。若为硬件损坏,需更换同型号编码器,并重新校准机械零点;若为信号干扰,需增加磁环滤波器或采用屏蔽电缆。
第二步:驱动器“参数调优”
采用“逐步逼近法”调整驱动器参数:
降低增益:若定位时出现振荡,可适当减小位置环增益,提升系统稳定性;
优化滤波:启用驱动器内置的数字滤波功能,抑制高频噪声;
负载匹配:根据负载惯量重新计算加速度、减速度参数,避免电机过载。
第三步:机械结构“全面体检”
针对机械故障,需开展以下检查:
传动链检测:使用激光对中仪校准联轴器同轴度,测量丝杠间隙是否超标;
导轨修复:检查导轨表面磨损情况,必要时重新刮研或更换;
紧固件复查:紧固所有传动部件螺栓,避免因松动引发位移偏差。
行业倡议:构建“软硬件协同”维修体系
维修专家强调,伺服电机定位偏差的本质是系统耦合故障。企业应建立以下机制:
预防性维护:每季度对编码器进行清洁与信号测试,定期校准机械零点;
参数数据库建设:记录不同负载工况下的最佳参数组合,实现快速调参;
机械健康监测:在关键传动部件安装振动传感器,通过AI算法预测磨损趋势。
当前,伺服电机作为精密制造的“神经中枢”,其定位精度直接关乎产业竞争力。工控维修行业呼吁企业摒弃“头痛医头”的被动模式,转向“软硬件协同优化”的主动策略,以技术革新与制度保障护航智能制造升级。
转载请注明出处:上海仰光电子科技专业伺服驱动器维修,伺服电机维修
本文链接:http://www.shygdz.com/fuwu/Services_Show35548.htm
伺服驱动器维修 伺服电机维修 触摸屏维修 变频器维修
联系方式:
电话:021-50157782
手机:13817011982 微信同号
邮箱:shygdzi@163.com
联系人:张工
网址:http://www.shygdz.com
【 我们确保修好测试好给客户!!!!】
上一篇:伺服电机维修警报:驱动、电机与信号异常成“停摆”主因
下一篇:没有了